What Is A Toolbox Talk?
A toolbox talk is an informal group discussion that focuses on a particular safety issue. These can be used to promote department safety culture as well as to facilitate health and safety discussions on job sites.
Benefits of Toolbox Talks?
A safer workforce is a healthier workforce, and a healthier workforce is a safer workforce. Below are a few examples of benefits that regular toolbox talks can have at your workplace.

Increases safety awareness
Injury risk is always present in the workplace, regular toolbox talks can help increase awareness and ensure that everyone is on the same page when it comes to safety and protocols and carrying out safe work practices. It also can assist with regular refreshing of safety knowledge which can easily be overlooked.
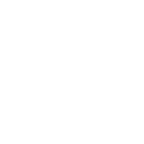
Reduces Workplace Injuries
Taking part in regular toolbox talks ensures that safety is top of mind. This helps to reduce the number of workplace injuries, keep workers safe at work and get them back home safely each day. Toolbox talks can also be used to convey messages of safe manual handling practices and other safety practices which reduce injury rates.
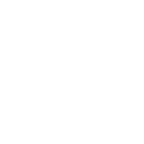
Promotes Team Communication
Toolbox talks also give you a chance to raise any health and safety concerns with your supervisors as well as address any gaps in your safety knowledge. It is also an opportunity for questions, queries or concerns to be raised by the team.
It’s Time To Reduce Sprain & Strain Claims
Toolbox talks are a great way to educate workers about risk management and reducing sprain and strains. Specific topics such as manual handling techniques and learning to identify risks can be covered in your toolbox talks to assist with lowering claim rates.
How can we help you?
Please leave your details and one of our representatives will be in touch within 24 hours. If you have an urgent request, please call us on 0800 442 572
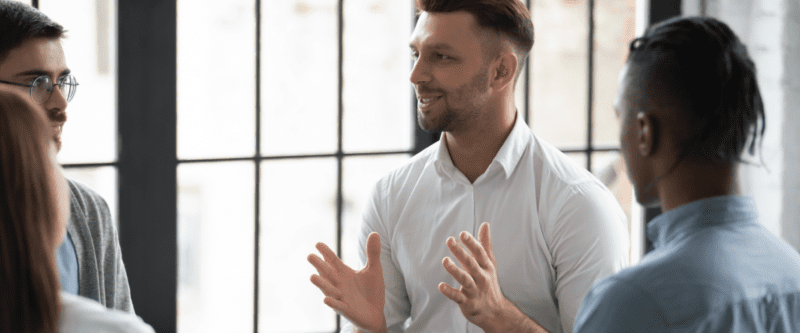
What Does A Toolbox Talk Include?
Toolbox talks include informing workers about new plant equipment, work practices or systems and helps a workplace to eliminate or minimise hazards from the beginning. Toolbox Talk topics provide information about common workplace hazards along with guidance for other leadership members.
Toolbox Talk Topics
Confined Spaces Toolbox Talks
Typically we think of warehouses as large, open spaces, but warehouses can also include confined spaces thanks to tightly packed and stacked boxes. Employees should understand the difference between permit-required and non-permit-required confined spaces and the behaviours that keep them safe when working in them.
Ergonomics Toolbox Talks
Hazardous manual handling is one of the biggest causes of injuries in New Zealand workplaces, partly because they happen so easily. An object doesn’t need to be that heavy to cause serious damage if it’s not handled properly. In fact, you could be sitting awkwardly at your desk right now and not even know it.
Slips Trips and Falls Toolbox Talks
Slips, trips and falls are a common reason for industrial injuries. General housekeeping goes a long way to preventing these accidents. Leaks and spills should be cleaned up immediately and broken planks and tiles fixed as a priority.
Chemical Safety Toolbox Talks
Do you know which chemicals are used around your workplace? What would you do if you came into contact with one? If your team isn’t aware of the situations that can occur when chemicals aren’t stored and used safely, now’s a great time to discuss it.
Hearing Protection Toolbox Talks
Ear protection helps to protect your hearing from damaging noise that may be present at any given time around you. Long exposure to these loud noises can cause serious long-term damage that only gets worse over time; so protecting your ears is an important part of protecting your hearing from these damaging noises.
Asbestos in Construction Toolbox Talks
Asbestos-containing materials are still present in many buildings that were built before the year 2000. Construction workers may come across these during their work. If people need to carry out work around asbestos-containing materials, your toolbox talk first thing that day could involve refreshing their knowledge of asbestos risks and what they should or shouldn’t do to prevent exposure.
Extension Cord Toolbox Talks
Working safely with electricity has also allowed us to advance in all areas, and it’s in our modern-day nature to expect things to work with a flick of a switch. But do you know how many vaults are flowing through each tool or piece of equipment? Extension cords – how to check the cord for damage or frayed insulation, protecting cords from damage while using them, placing cords properly or covering them to avoid creating a trip hazard etc.
Why Employ Health?
We know your workplace
As onsite physios our toolbox talks aren’t generic, Employ Health physiotherapists have the opportunity to understand how your business works and what the injury risks are, meaning more specific tailored toolbox talks.
Develop Relationships with Workers
Attending regular toolbox talks allows Employ Health to continue developing rapport and relationships with key stakeholders and workers.
Promote Employ Health Projects and Services
Toolbox talks are also a great opportunity to promote any services or projects that are running onsite, giving workers an opportunity to ask questions.
Frequently Asked Questions
It is a legislative requirement to consult and communicate with workers on health and safety matters and also very good practice, so toolbox talks are the perfect way to do this.
This can depend on the size and requirements of the workplace but often 1-2x a week is common.
Health and safety managers and advisers are generally best equipped to evaluate the information reported in toolbox talks, this includes ensuring that important information and topics are covered as well as answering questions from workers.